DTF printing is a revolutionary technique that has gained significant attention in the printing industry. With its ability to produce high-quality and detailed prints on various materials, this printing has become a popular choice for businesses and individuals alike. In this article, we will explore the concept of direct-to-film printing, understand its process, advantages, and applications, and compare it with other printing methods.
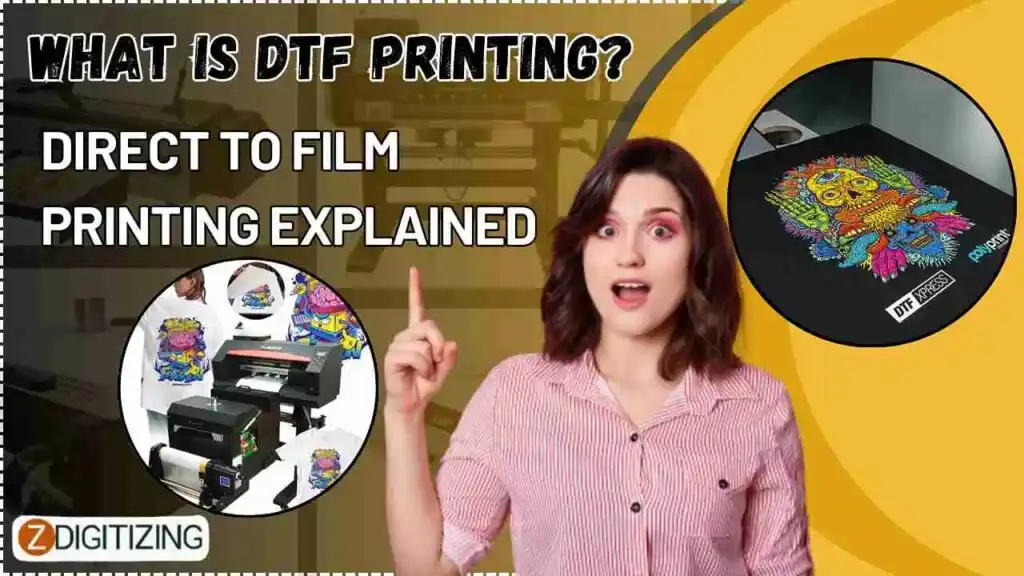
What is DTF Printing?
What is DTF Printing?
DTF transfer printing refers to a method where designs are printed onto a special film, which is then transferred onto various fabrics using heat and pressure.
This technique allows for high-quality, durable prints and is particularly useful for complex color applications and small-batch orders. Unlike traditional methods, it doesn’t require extensive setup, making it an efficient choice for custom textile decoration.
How Does Direct to Film (DTF) Printing Work?
DTF involves a process where designs are first printed onto a clear film using specialized DTF printing machines. This technique employs a unique kind of ink that, when printed, is transferred to the film.
The printed film is then coated with a powdered adhesive which plays a crucial role in the transfer process. The prepared film is applied to the fabric under heat, causing the adhesive to activate and bind the ink to the fabric, effectively completing the print DTF process.
This method enables vibrant, high-resolution designs to be efficiently applied to a variety of textiles. The process is valued for its ability to produce detailed and color-rich images with a high level of durability and washability.
Embroidery Digitizing & Vector Art Services
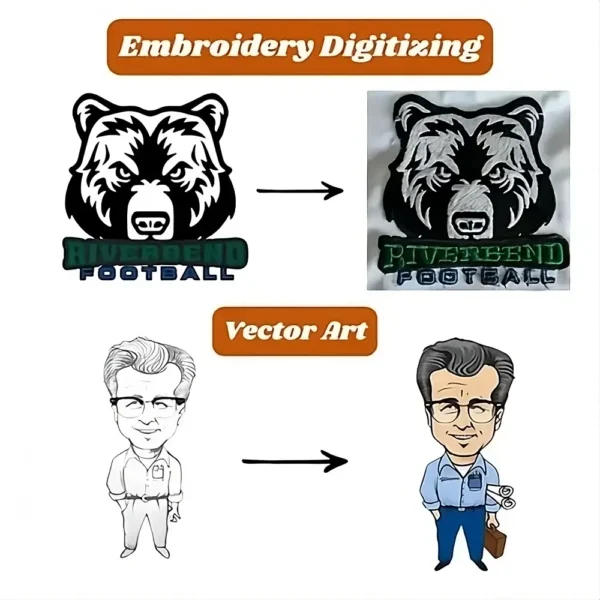
Looking for embroidery digitizing and vector art services that are affordable and reliable? We offer fast turnaround time, guaranteed quality, and the option to preview your design before payment, we make sure you get exactly what you need. Your satisfaction is our top priority, and we’re dedicated to delivering the best results. Don’t wait—try ZDigitizing today and see the difference in quality and service!
Embroidery Digitizing & Vector Art Services
Looking for embroidery digitizing and vector art services that are affordable and reliable? We offer fast turnaround time, guaranteed quality, and the option to preview your design before payment, we make sure you get exactly what you need. Your satisfaction is our top priority, and we’re dedicated to delivering the best results. Don’t wait—try ZDigitizing today and see the difference in quality and service!
Benefits and Limitations of Direct to Film Printing
It encompasses several aspects that range from highly advantageous to potentially restrictive, influencing its adoption across various industries.
Benefits of DTF Transfer Printing
- Versatility in Fabric Compatibility: Can print on a variety of fabrics, including challenging blends, without the need for pre-treatment.
- High-Quality Prints: Capable of producing intricate and colorful designs that maintain their quality even after multiple washes.
- Cost-Effectiveness for Small Runs: Ideal for small to medium-sized print batches, minimizing setup costs compared to traditional printing methods.
- Ease of Customization: Supports high levels of customization, making it perfect for bespoke orders and limited-edition products.
Limitations of DTF Transfer Printing
- Initial Investment Cost: High startup costs due to the need for specialized DTF printing machines and materials.
- Labor-Intensive Process: Multiple steps including printing, powder application, and heat transfer require more manual labor compared to direct print methods.
- Environmental Concerns: Uses plastic films and synthetic adhesives, raising sustainability and disposal issues.
Technical Complexity: Requires technical knowledge to manage the full process effectively, from design setup to final heat press application.
Materials and Equipment Needed for Direct-to-Film Printing
To start with DTF shirt printing, you’ll need a few specific materials and pieces of equipment. This setup ensures that you can create high-quality prints efficiently.
Materials
Printable Film: A special type of clear film that your designs will be printed on.
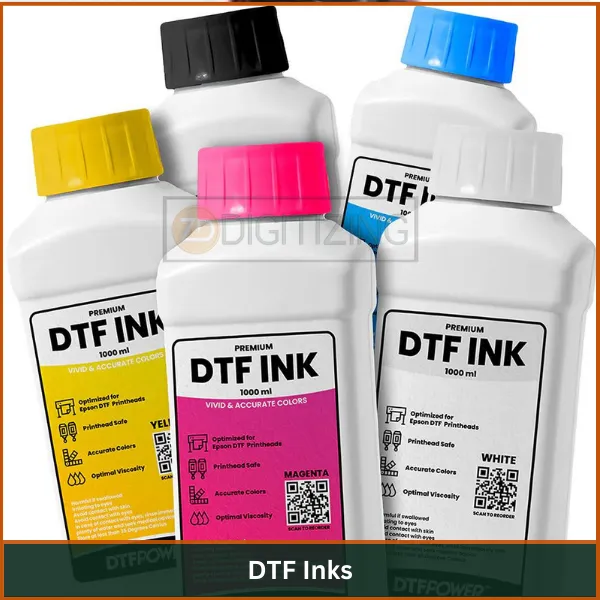
DTF Inks: These are specially formulated inks used for printing on films, compatible with the color and texture requirements of DTF printing.
Powder Adhesive: After printing, a fine powder adhesive is applied to the ink on the film. This adhesive is crucial as it helps the design adhere to the fabric during the transfer process.
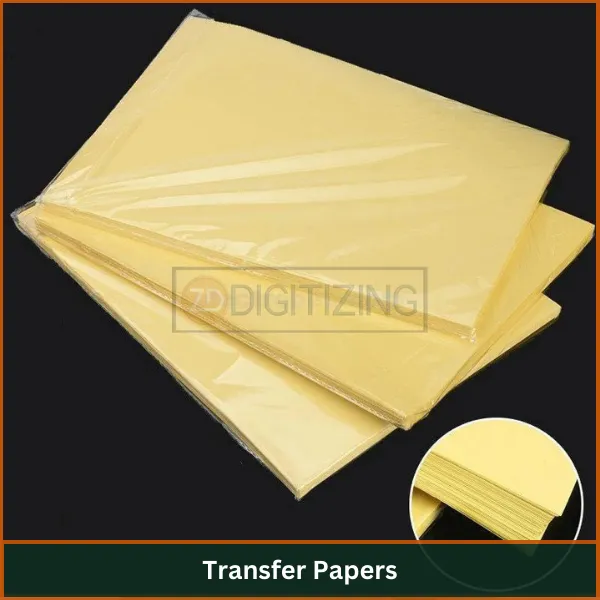
Transfer Papers: To move the printed design from the film to the shirt, transfer papers are used.
Equipment
DTF Printer: A printer specifically designed for direct-to-film printing. It can handle the inks and films used in DTF processes.
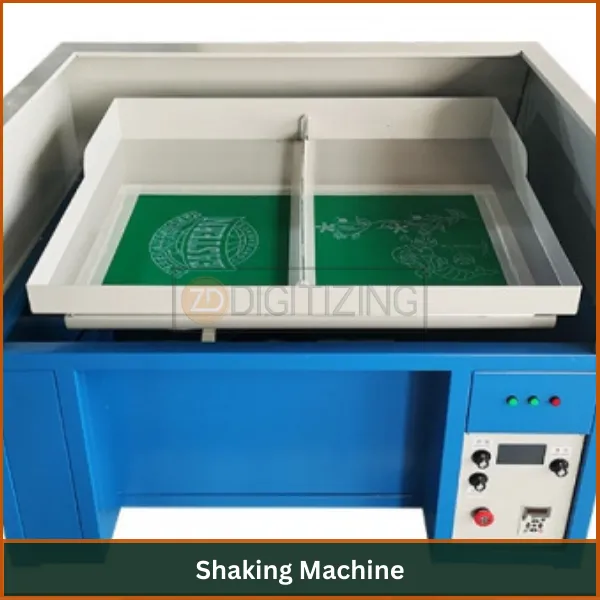
Shaking Machine: This machine evenly distributes and cures the adhesive powder on the printed film.
Heat Press: A heat press is used to transfer the design from the film onto the shirt. The heat activates the adhesive, securing the ink to the fabric.
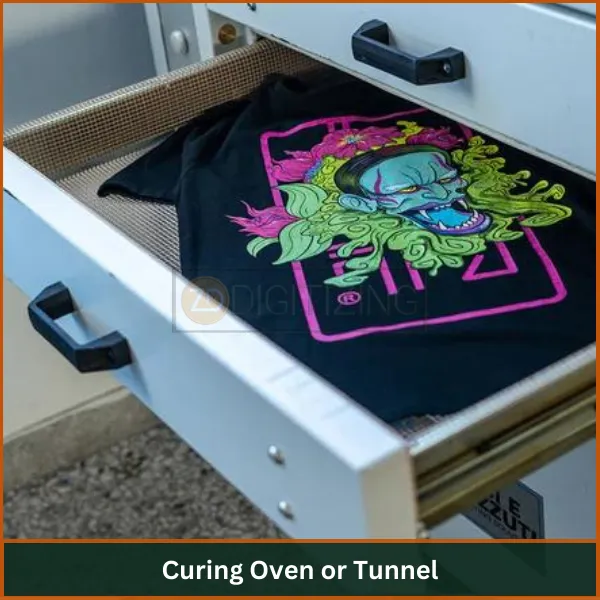
Curing Oven or Tunnel: After the print is transferred, a curing oven or tunnel is used to set the ink permanently onto the fabric.
With these materials and equipment, you can start your DTF transfer printing projects and create vibrant, durable designs on shirts and other textiles.
How to Do DTF Printing? | Step-by-Step Process
The process of DTF transfer printing involves several key steps from start to finish. Each step is crucial for ensuring high-quality, durable prints on various textiles.
Step 1: Prepare Your Design
First, create or choose your design using graphic design software. If you’re looking for top-notch designs that stand out, consider using our professional vector art services at ZDigitizing.
Our designs ensure high resolution and are perfectly formatted for DTF, making your products truly unique and appealing.
This is an ideal solution to enhance the quality of your prints, and many customers have seen remarkable results by integrating our custom designs into their DTF process.
Step 2: Print the Design on Film
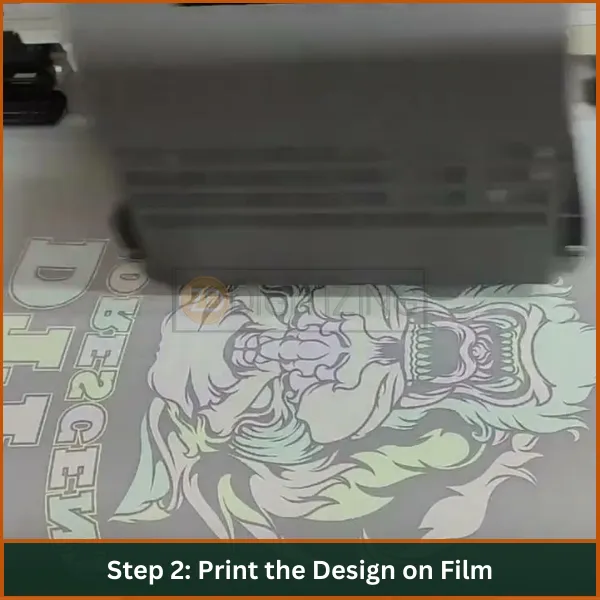
Load the DTF printer with the special DTF film and choose the right settings for your specific design. Use DTF inks to print the design directly onto the film. The ink should be applied evenly across the design to ensure consistent quality.
Step 3: Apply Powder Adhesive
Once the design is printed on the film, apply a layer of powder adhesive over the wet ink. This can be done manually or with a shaking machine, which helps distribute the powder evenly. The adhesive is crucial for bonding the ink to the fabric later.
Step 4: Cure the Print
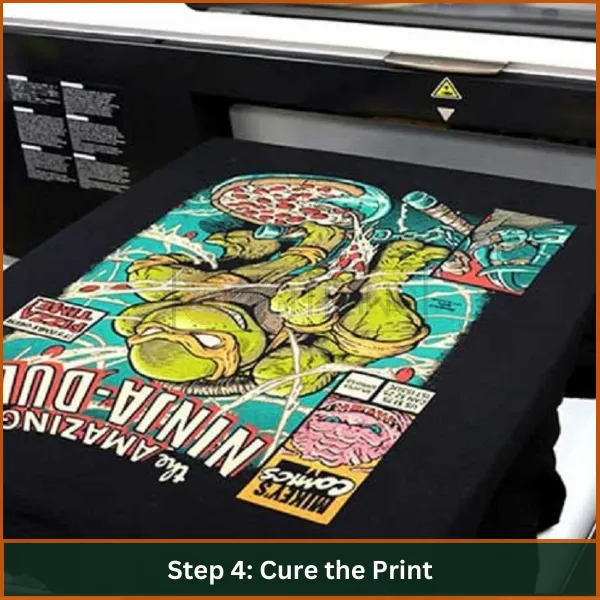
Transfer the film with the design and adhesive into a curing oven or under a heat lamp. The heat will cure the adhesive, setting it in place and preparing it for the transfer. This step solidifies the adhesive to ensure it binds well with the fabric.
Step 5: Heat Press the Design onto Fabric
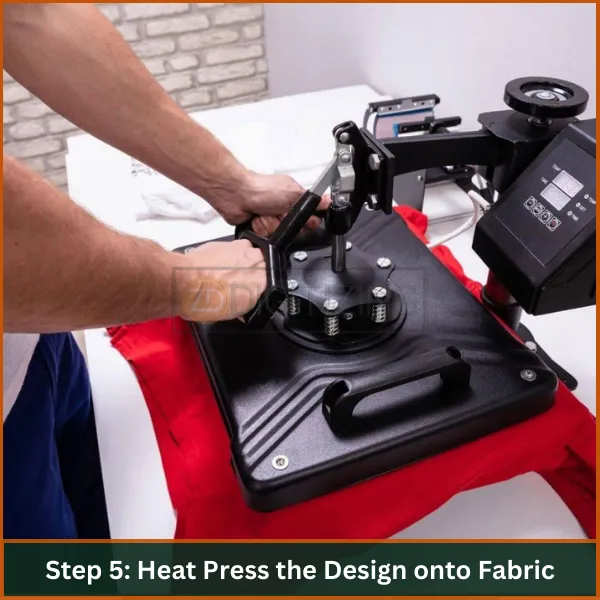
Preheat your heat press to the required temperature. Place the film on the fabric, design side down, and position it correctly. Press the film onto the fabric using the heat press. The heat activates the adhesive, causing it to bond the ink firmly to the fabric.
Step 6: Peel and Finish
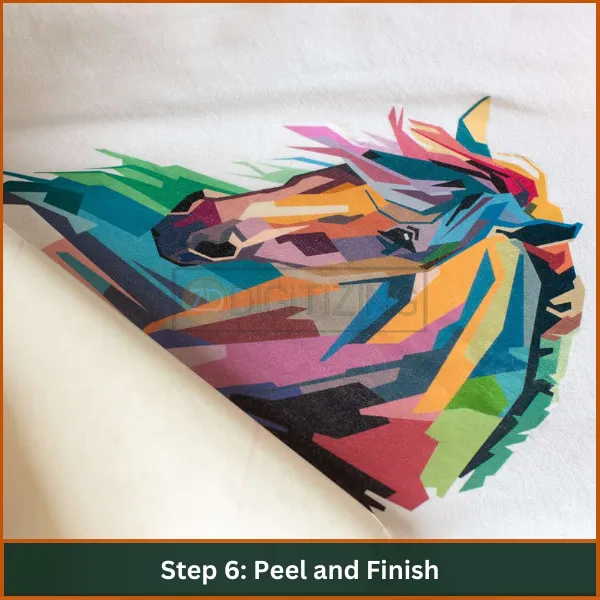
After pressing, allow the fabric to cool slightly, then peel off the film. The design should now be securely transferred to the fabric. If necessary, you can repress the fabric with a protective sheet to ensure the print is fully set.
Step 7: Final Curing
Some DTF processes require a final post-press cure, either in a tunnel or under a heat lamp. This step ensures that the print is completely cured and set into the fabric, enhancing its durability and washability.
Troubleshooting Common Issues During DTF Printing
It can encounter various challenges that may affect the quality of the final product. Here are some common issues and their solutions to help ensure smooth and efficient printing operations:
Ink Not Adhering to the Film
- Problem: Ink may not stick if the film isn’t specifically for DTF use or the printer settings aren’t correctly adjusted.
Solution: Use proper DTF-specific films and adjust your printer settings to ensure compatibility with the ink and film being used.
Poor Quality of Final Prints
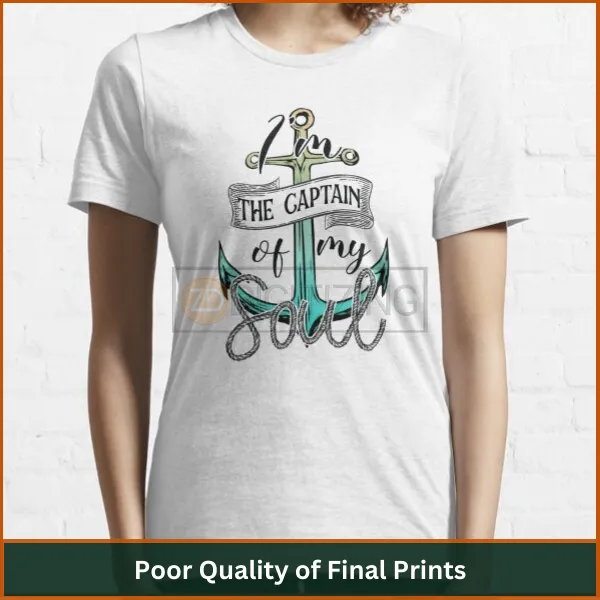
- Problem: Blurry or incomplete prints can result from low-resolution designs or clogged printer nozzles.
- Solution: Ensure your design files are high resolution and perform regular maintenance and cleaning of printer nozzles.
Adhesive Powder Not Sticking
- Problem: Adhesive powder may not adhere if applied after the ink has dried or if affected by the environment’s humidity.
- Solution: Apply the adhesive powder while the ink is still wet and ensure the printing environment’s humidity is controlled.
Color Inconsistency
- Problem: Inconsistent colors can occur due to uncalibrated printers or variations in ink quality.
- Solution: Regularly calibrate your DTF printer and use high-quality, consistent DTF inks for printing.
Film Peeling Off During Heat Press
- Problem: The film may peel off if the heat press settings, like temperature and pressure, are not correctly set.
- Solution: Adjust the heat press temperature and pressure settings to ensure even and adequate heat is applied for the transfer process. Ensure the heat press is properly maintained for consistent performance.
Application of Direct-to-Film Printing
Direct-to-film (DTF) printing offers versatility across various industries and applications. Here are some of the key uses:
- Custom Apparel: Ideal for creating unique designs on t-shirts, hoodies, and other garments, especially for small to medium-sized batches.
- Fashion Accessories: Applied to bags, hats, and shoes, DTF printing allows for detailed and colorful embellishments.
- Home Décor: Used to print on cushion covers, curtains, and other fabric-based home décor items to add personalized touches.
- Sportswear: Provides durable prints that can withstand the rigorous demands of sportswear, including jerseys and athletic gear.
- Promotional Items: Perfect for creating customized promotional products like flags, banners, and corporate apparel that require high-quality prints.
- Prototype Samples: Useful in the design process for fashion and textiles, allowing designers to produce and test patterns before mass production.
Embroidery Digitizing & Vector Art Services
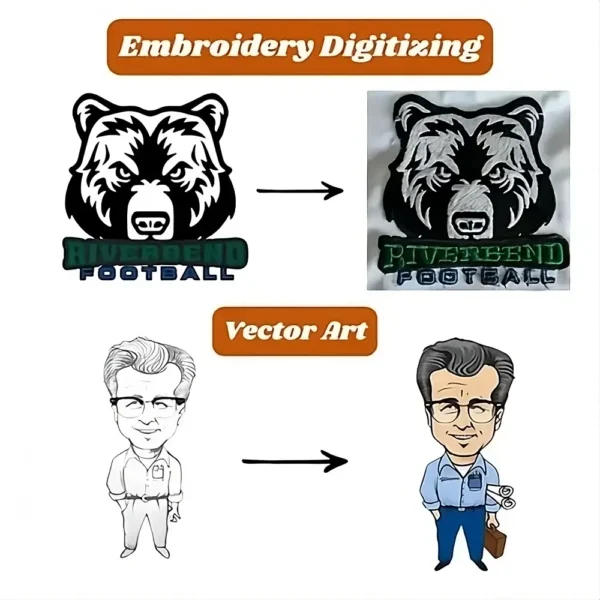
Looking for embroidery digitizing and vector art services that are affordable and reliable? We offer fast turnaround time, guaranteed quality, and the option to preview your design before payment, we make sure you get exactly what you need. Your satisfaction is our top priority, and we’re dedicated to delivering the best results. Don’t wait—try ZDigitizing today and see the difference in quality and service!
Embroidery Digitizing & Vector Art Services
Looking for embroidery digitizing and vector art services that are affordable and reliable? We offer fast turnaround time, guaranteed quality, and the option to preview your design before payment, we make sure you get exactly what you need. Your satisfaction is our top priority, and we’re dedicated to delivering the best results. Don’t wait—try ZDigitizing today and see the difference in quality and service!
Comparison of DTF Printing with Other Printing Methods
Feature | DTF | DTG | Screen |
Method | Transfers from film to fabric | Direct inkjet on fabric | Ink through stencils |
Fabric Compatibility | Multiple types, including blends | Best on cotton | All fabrics |
Color Vibrancy | High, slightly raised | High, less raised | Very vibrant, and textured |
Setup Cost | Moderate | High | High |
Production Speed | Moderate | Slow | Fast |
Durability | Excellent | Good | Very durable |
Setup Complexity | High | Moderate | High |
Batch Efficiency | Good for small-medium | Best for small | Good for large |
Eco Impact | Less eco-friendly | More eco-friendly | Potentially harmful |
Conclusion
In conclusion, DTF printing has revolutionized textile decoration, making it easier and more efficient to transfer detailed, vibrant designs onto various fabrics.
If you’re considering starting a project involving this printing method, or if you need unique designs, explore our professional vector art services at ZDigitizing. We provide the benefits of swift project completion, competitive pricing, and superior quality, ensuring your fabric prints look outstanding.
Moreover, we’re offering a special 50% discount for our first-time clients. Take advantage of this offer to enhance your textile projects with top-notch designs that truly stand out!
FAQs
Direct to Film (DTF) printing is known for its durability and long-lasting quality. The prints typically withstand numerous washes without fading or peeling, making them a reliable choice for fabric printing.
Whether DTF is better than sublimation depends on the application. DTF works on a wide range of fabrics, including cotton, and offers vibrant color and texture. Sublimation, however, is best for polyester fabrics and offers a more integrated, dye-like finish.
The main disadvantages of DTF printers are the initial investment cost and the ongoing expense for specialized inks and transfer films. They also require a specific process for printing and transferring, which might be complex for beginners.
DTF can be more cost-effective than screen printing for small to medium runs due to lower setup costs and the ability to print detailed designs without the need for multiple screens. However, for large-volume orders, screen printing might be more economical.
Direct to Garment (DTG) prints can fade over time, especially with frequent washing and improper care. However, when properly printed and cared for, DTG prints can remain vibrant for a considerable amount of time.