In this article we will discuss top 10 compelling reasons you must know in order to need custom embroidery digitizing.
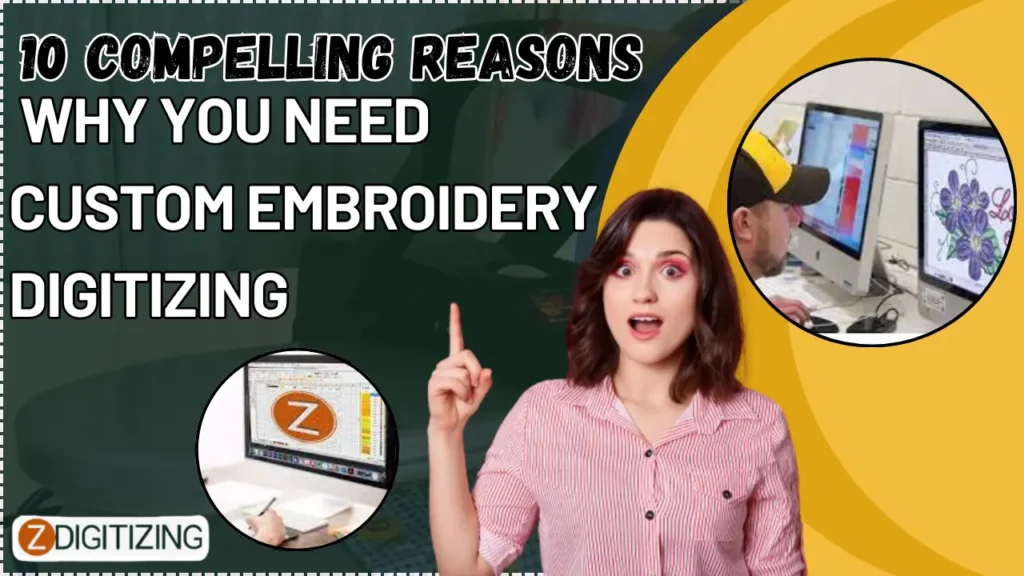
10 Compelling Reasons Why You Need Custom Embroidery Digitizing
10 Compelling Reasons Why You Need Custom Embroidery Digitizing:
Embroidery has been an art form for centuries, but with the advent of technology, custom embroidery digitizing has revolutionized the industry. This custom digitizing Embroidery Business process involves converting intricate embroidery designs into digital digitizing embroidery files, allowing for precise and efficient stitching on various fabrics. If you’re still unsure about the benefits of custom embroidery logo digitizing, let’s explore ten compelling reasons why you should consider it for your embroidery projects.
1. Unmatched Precision and Detail:
Custom embroidery digitizing involves converting intricate Embroidery designs into digital files that embroidery machines can interpret. This digitizing embroidery process ensures that every stitch is placed with utmost precision, capturing even the smallest details of the design.
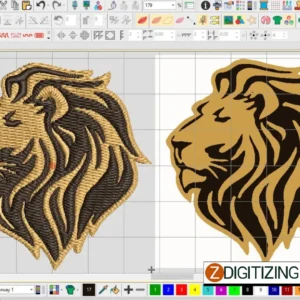
Unlike manual embroidery, which can be prone to human error, logo digitizing guarantees consistent and accurate results.
2. Versatility in Design:
Digitization allows for a wide range of embroidery design possibilities. From logos and monograms to complex artwork and intricate patterns, custom embroidery digitizing can transform any image or design into a stunning embroidery piece.
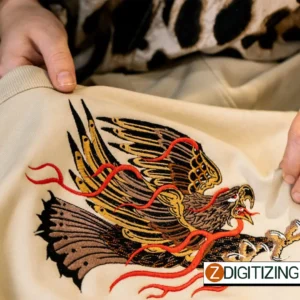
This versatility makes it suitable for various industries, including fashion, promotional products, and corporate branding for embroidery business.
3. Time-Efficient Production:
One of the significant advantages of custom embroidery digitizing is its time efficiency. Once the embroidery design is digitized.
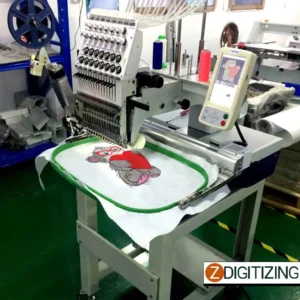
The embroidery machine can quickly replicate it on multiple items simultaneously. This expedites the production process, making it ideal for large-scale orders and tight deadlines.
4. Consistency in Replication:
Custom logo digitizing ensures that the same design can be replicated consistently across multiple pieces.
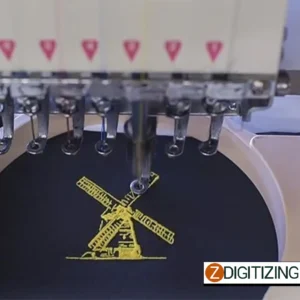
Each item will have the same level of detail and precision, maintaining brand consistency and overall quality. This is especially crucial for businesses that require uniformity in their embroidered products.
5. Wide Range of Fabric Compatibility:
Digitizing embroidery allows for adjustments based on the fabric type and texture.
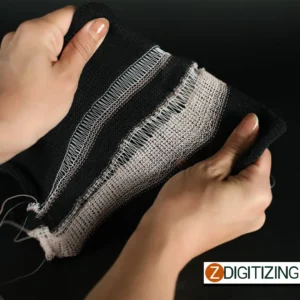
Whether it’s delicate silk, sturdy denim, or stretchy knits, the digitized embroidery file can be tailored to suit the specific fabric. This ensures that the design looks impeccable on any material.
6. Enhanced Branding:
Custom embroidery digitizing offers embroidery businesses the opportunity to embroider their logos, brand elements, and promotional messages on various products.
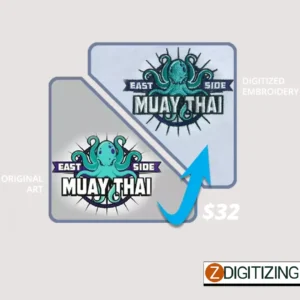
This enhances branding efforts, as embroidered logos leave a lasting impression on clients and customers. It also creates a sense of professionalism and credibility.
7. Personalization and Customization:
Digitizing empowers individuals to add a personal touch to their clothing and accessories.
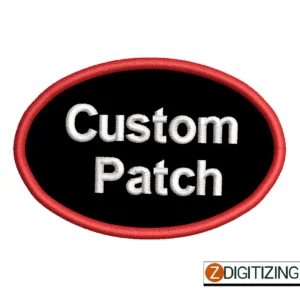
Whether it’s monogramming initials on a handkerchief or embroidering a custom design on a jacket, embroidery digitizing allows for unique expressions of style and individuality.
8. Increased Durability:
Embroidery digitizing results in tightly interwoven stitches, making the designs more durable and long-lasting. The strong bond between the threads ensures that the embroidery remains intact even after multiple washes and extended wear.
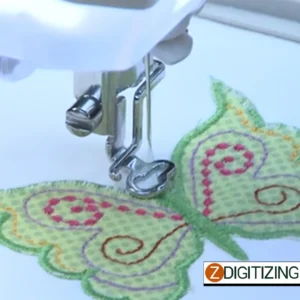
This durability is particularly advantageous for workwear, uniforms, and outdoor apparel.
9. Cost-Effective Solution:
While the initial investment in digitizing software and equipment may be required, the long-term cost savings are substantial.
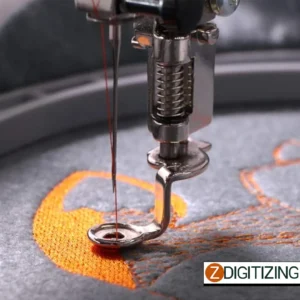
The efficiency of machine embroidery reduces labor costs, making it an economical choice for businesses and individuals with significant embroidery needs.
10. Artistic Freedom:
Custom digitizing offers embroiderers a platform for artistic expression and experimentation. Designers can play with various colors, stitch types, and textures to create unique and visually captivating embroidery pieces.
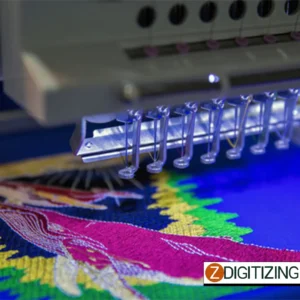
This artistic freedom pushes the boundaries of embroidery art and opens up endless possibilities for creative designs.
Helpful Tips For Custom Embroidery Digitizing:
Here are some helpful tips for custom embroidery digitizing:
- Look for an experienced and skilled digitizer who understands your specific embroidery needs. A proficient digitizer can bring out the best in your designs and ensure a smooth embroidery process.
- Keep in mind the size of the design and the intended application while digitizing. Large, intricate designs may not work well on small items, and vice versa. Scale the design appropriately to maintain its visual impact.
- Consider the type and quality of threads used for embroidery. High-quality threads ensure vibrant colors and enhanced durability. Choose the threads that complement the fabric and design.
- Before proceeding with bulk production, always test the digitized design on a sample fabric. This helps identify any potential issues and allows adjustments to be made if needed.
- While digitizing intricate designs is possible, it’s essential to simplify complex elements for better results. Avoid excessive layering and overlapping, as it may lead to stitching issues.
- Proper stitch density is crucial for a well-executed embroidery. Too few stitches can result in a sparse design, while excessive stitches can cause puckering and stiffness. Aim for a balanced stitch density.
- Incorporate underlay stitches to stabilize the fabric before the main design. Underlay stitches improve design registration and prevent shifting during embroidery.
- Choose the appropriate backing material and stabilizer for the fabric type. Additionally, maintain proper thread tension to prevent thread breakage and ensure clean embroidery.
- Utilize the latest embroidery digitizing software and keep up-to-date with new features and tools. Modern software offers advanced options for better design control.
- Thoroughly review the digitized design before production. Pay attention to details like stitch direction, alignment, and color choices. Address any issues to achieve a flawless final result.
- Provide the digitized design in various file formats to accommodate different embroidery machines and software used by manufacturers or clients.
- Regularly back up your digitized designs to prevent data loss and ensure continuity in case of technical issues.
- Different fabrics require different approaches to digitizing. Adjust stitch lengths and densities based on the fabric’s texture and thickness to achieve optimal results.
- Anticipate how the design will look in different color variations. Provide multiple color options to offer clients more choices for their embroidered products.
- While automatic digitizing tools are helpful, manual editing may be necessary for complex designs or specific details. Fine-tune individual stitches to perfect the design.
- If you’re digitizing designs for a collection or a series of products, strive for consistency across all designs. Uniformity in style and size enhances brand identity.
- Jump stitches are long threads that connect design elements without stitching them together. Minimize jump stitches to reduce the need for trimming and create a cleaner finish.
- Pay special attention to digitizing letters and fonts. Ensure they are clear, legible, and well-proportioned for the intended size and application.
- If possible, test your digitized designs on various embroidery machines to ensure compatibility and consistent results across different equipment.
- Utilize layers in your digitizing software to organize complex designs effectively. Separating design elements into layers simplifies editing and makes it easier to manage the entire design.
- When digitizing gradients or blends, practice blending techniques to achieve smooth transitions between colors and shades.
- While editing is essential, be cautious not to over-edit the design, which can lead to excessive density or loss of design integrity.
- When digitizing designs based on existing artwork or logos, ensure you have the right to use the design and respect copyright laws.
- Keep an eye on emerging trends in the embroidery industry, such as new stitch styles, textures, and effects, to offer innovative and up-to-date designs.
- Continuously improve your digitizing skills by practicing regularly and seeking feedback from experienced digitizers or clients.
Winding Up:
In conclusion, custom embroidery digitizing revolutionizes the embroidery industry by combining technology with artistry. The process offers unmatched precision, versatility, and time-efficiency, making it a preferred choice for businesses and individuals alike. From consistent replication to increased durability, digitization elevates embroidery to new levels of craftsmanship and beauty, leaving a lasting impact on the world of textiles and fashion.
Looking for top-notch embroidery design digitization? Look no further than ZDigitizing! We are a trusted and professional company offering comprehensive digitizing and vector art services worldwide. With fast turnaround times and unmatched quality, ZDigitizing is your ultimate choice for all digitizing needs. Get a free quote in under 5 minutes and enjoy an exclusive 50% discount on your first order. Don’t miss out on this fantastic opportunity!
If there’s any question related to this article you can simply ask in the comment section and don’t forget to share with those you think might be helpful for them.
And finally, thanks for reading!
Frequently Asked Questions:
Custom embroidery digitizing offers the advantage of turning unique designs into embroidery files, allowing for personalized and exclusive creations. It enables precise detailing, color control, and scalability, ensuring that each embroidered piece is tailored to the customer’s specific requirements.
Embroidery digitizing can be challenging, requiring technical expertise, artistic vision, and proficiency in specialized software. It involves translating complex artwork into stitch instructions, considering factors like stitch types, density, and sequencing to achieve high-quality results.
The primary purpose of embroidery is decorative embellishment. It adds artistic elements and logos to various textiles, enhancing their visual appeal. Additionally, embroidery can also serve functional purposes, such as reinforcing fabric, as seen in traditional hand-sewn techniques.
To digitize and embroider a design, first, the artwork is converted into a digital embroidery file using specialized software. The digitized file contains stitch instructions for the embroidery machine. When executed, the machine follows these instructions to stitch the design onto the chosen fabric.
Digitizing transforms artwork into a language that embroidery machines understand. It’s a crucial step that converts the design into stitch data, determining stitch types, colors, and order. Digitizing ensures precise replication of the artwork in the final embroidered product.